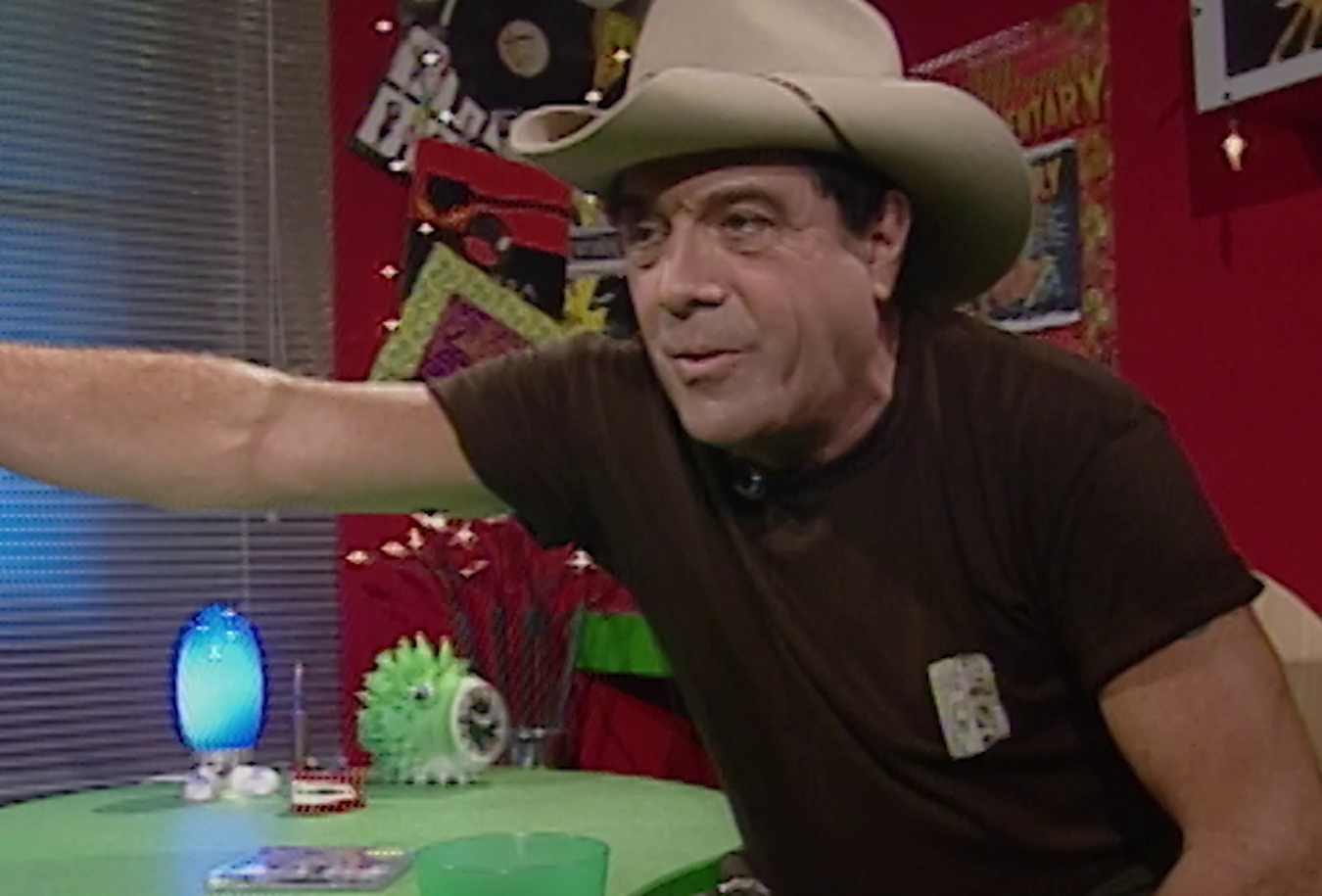
I’m currently studying Mechanical Engineering at RMIT University, Melbourne and working as a cadet with the NFSA, focusing on incorporating my academic and technical knowledge to improve the functionality of machinery and legacy equipment.
Being an engineer in the NFSA is challenging when some of the equipment used to preserve and restore materials in the collection is as old as the materials themselves.
Frequently, we find that legacy equipment doesn’t have manuals or they are hard to find; information about these machines online is limited or non-existent; the company that originally produced them may no longer exist; and spare parts are a rarity. It requires ingenuity and innovation to fix any issues using available and equivalent parts in place of defunct ones.
Maintaining legacy equipment is as important as preserving the audiovisual media played and recorded on them. They aren’t items you can pop down to a store and pick up, or buy from eBay in a fully functional condition. They are no longer being manufactured and without them, how are future generations going to play back the original medium, let alone continue with preservation work? I am lucky to have colleagues with a wealth of knowledge about the collection and this equipment. Documenting this information and sharing it with the next generation is becoming more critical as time passes.
Recently, I was asked to do some maintenance work on the Intercine, a four-reel flatbed film viewer that was purchased by the NFSA in 1980. My colleagues in the Film Services team want to resume using the Intercine to examine film, but the machine wasn’t transporting the film properly, in a way that they would feel confident using shrunken film on it.
They showed me how to lace a 16mm print and operate the Intercine. A thorough internet search yielded minimal results: a video on how to clean areas that came in contact with the film; trademark information on Intercine Universal, the parent company. A fellow engineer advised that it was unlikely that there would be a manual; it was his understanding that each viewer was unique. This was the extent of the knowledge I was armed with, and I was understandably nervous.
My nerves faded after spending some time with the Intercine. I laced a disposable piece of film to see how the machine ran. Without knowing exactly what is wrong with a piece of equipment, or having prior knowledge of its faults and maintenance, you can discover potential issues simply by listening for unusual sounds, or feeling resistance where there should be little or none.
The Intercine’s fault wasn’t immediately obvious from a quick look under the hood. Luckily, there turned out not to be anything critically wrong with it. A few bearings in the guide rollers sounded dry, but that was nothing that a good clean and grease wouldn’t fix. An on/off switch and a potentiometer used to control the bass level in the audio control box had broken levers, but the whole component is easily replaced.
A final run through of a junk film showed the Intercine to run like a dream, smoothly transporting the film and sounding clearer than before.
Throughout the process, I made a point of documenting what I’d done, and explaining the function of each button, switch and lever. However, preserving legacy equipment isn’t always as easy as replacing a few readily available parts. More often than not, it’s the surprise or intermittent failure that requires the most attention and ingenuity. Decades ago, the information was readily available. A manual came with the machine upon purchase, and problem solving was as simple as contacting a company representative for advice or parts.
Now we are the experts – or in my case, working hard to become an expert. We are using our knowledge base to understand the equipment, being aware of which parts are becoming hard to find and stockpiling accordingly. Documenting and sharing our knowledge will ensure that future generations will be able to use the equipment properly and continue preserving our audiovisual history.
The National Film and Sound Archive of Australia acknowledges Australia’s Aboriginal and Torres Strait Islander peoples as the Traditional Custodians of the land on which we work and live and gives respect to their Elders both past and present.